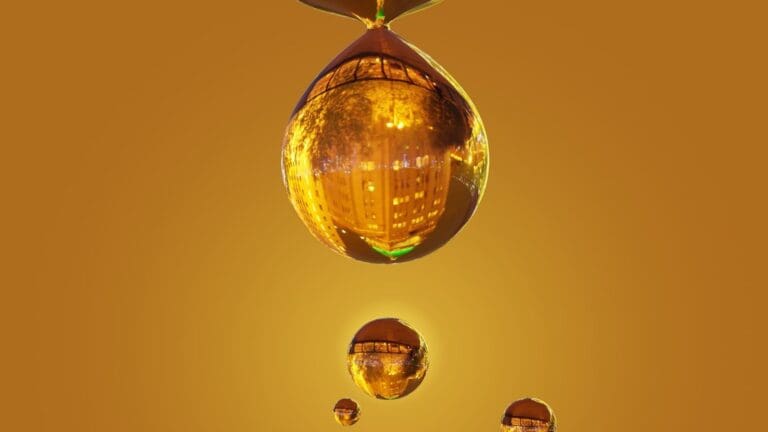
Over the same period, there have also been fundamental improvements to the specifics of C2 kerosene for fixed combustion as follows:
2010
• Introduction of first minimum and maximum density limits for C2 kerosene.
• Introduction of first minimum specific energy content value for C2 kerosene.
• Reduction in maximum sulphur content of C2 kerosene.
2017
• Minimum density limit of C2 kerosene increased from 750 kg/m3 to 775 kg/m3.
2023
• Reduction of maximum density limit of C2 kerosene from 840 kg/m3 to 820 kg/m3.
• Introduction of first maximum specific energy limit for C2 kerosene.
These improvements, which are essential in controlling the consistency of kerosene for fixed combustion purposes, are relatively recent introductions, as these timeline charts clearly demonstrate.
The reduction in sulphur resulted in changed flame luminosity and reduced fuel lubricity, both successfully addressed by adaptations introduced by burner component manufacturers.
In terms of kerosene density range, the heating sector now enjoys the tightest specification since the 1960s, and this has resulted in significantly improved fuel consistency. Density is also the primary factor affecting the specific energy of the fuel.
A consequence of the tightening of the density range is fixed maximum and minimum specific energy values, since these are calculated from the minimum and maximum density limits of the fuel. The resultant consistent density and specific energy enables a fixed combustion process to be set that is appropriate for every fuel delivery. Prior to this consistency, and without adjustments to the combustion process, any increase in specific energy would result in sooted-up boilers and a reduction in specific energy could create cold start issues due to excess air in combustion.
It is worthy of note that:
1. Over this 25-year period the kerosene specification regarding water has never changed, it has always been, and remains, ‘no visible water’. If water is found in a customer’s tank, then it should be considered as exactly that, “water in a customer’s tank” rather than “water in the fuel”, since water and oil do not mix.
Water (which leads to sludge) in tanks is predominantly due to condensation and/or water ingress into the tank. An essential part of every service visit is to check the tank for water and make the customer aware of any problem identified that requires rectification.
2. There is no permissible bio-content within BS 2869 Class C2 kerosene.
3. Premature carboning of vaporising sleeve burner combustion bases and/or Bundy tubes can be attributable to burner bases running hotter than they should below the sleeve burner. This may be due to insufficient flue draught (unlined and/or oversized stack) and/or insufficient fresh oxygenated combustion air supply (no air brick!).
Article compiled and submitted by Alan Black Oil Heating Consultancy Services Ltd.
BS 2869:2023 is available from https://knowledge.bsigroup.com/products/fuel-oils-agricultural-domestic-commercial-and-industrial-fixed-combustion-applications-specification?version=standard
Image credit: istock
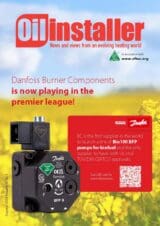